C20 notching press
See Video of C2O Notching Press Click Here.
See Video of Four Arm Automatic Feeder Click Here.
See video of robot fed C20 notching press. Click Here.
See C20 robot cell making 10 parts per minute. Click Here.
See 7 arm rotary notching cell 7AA. 7AA
Benefits:
- Fast 1000 stroke per minute notching speeds for typical laminations
- Slot accuracies of +/- 0.025mm (+/- 0.001″) as measured on a 840mm (33″) diameter, assure high accuracy lamination cores
- Tightly integrated computerized press controls are less complex than comparable controls of German notching presses. Positech controls are housed in enclosures that are less than HALF the size required by German notching presses.
- Compuslot® servo indexing for fast product changeovers; average changeover time is 15 minutes
- Automatic root diameter adjustment that is fast (15 seconds) and repeatable within 0.0002 inch.
- Simple to maintain without Positech assistance
- Low price
Features:
- Compuslot® servo indexer drives a high accuracy gearset running in an oil bath, inside a totally sealed gearbox.
- A separate servo controlled linear ball screw automatically sets the position of the indexing spindle to accommodate different lamination diameters between 150mm and 1320mm (4.5″ and 52″). Position settings are repeatable with 0.005mm (0.0002″).
- The controller calculates the maximum permissible stoking speed for each lamination part depending upon size and number of slots; a speed command is sent to a variable speed drive for the press flywheel motor.
- Programmable press speed reduction near end of each lamination stabilizes flimsy laminations
- Capability to notch skip-notch and skewed core patterns
- Capability to produce multiple slot patterns in each lamination.
- Preloaded linear roller bearings on the press slide accurately drive slot diesets and extend tooling life.
- A compact Desch-Lutex clutch-brake unit assures consistent press top-stops. This hardy unit is capable of over 6 million operating cycles on one set of linings. Linings can be quickly changed by factory maintenance personnel.
- The controller automatically sets the press top-stop position and compensates for different press speeds. No manual adjustments for press top-stop are required.
- A press brake monitor inhibits press operation if the press stopping time or distance falls outside of a pre-set limits.
- Press bearings are protected by a filtered, recirculating central press lube system. This delivers positive lubrication flow to each press bearing. A lube monitor inhibits press operation if there should be a lube system malfunction, or if the lube level in the reservoir is too low.
- Specifications for 400 lamination parts can be permanently stored in the controller.
- A piece counter totalizes the number of parts made.
- Ergonomic two hand anti-tiedown / anti-repeat operators “run-bar”station is provided.
- Point of operation guard is furnished to protect operating personnel near the dieset)
- A lamination hold down apparatus is provided to secure each lamination to its drive adapter
- A lamination stripper removes the lamination from the drive pins at the end of each notching cycle
- Notching speeds up to 1100 strokes per minute
C20 press specifications:
- Rated press capacity near BDC ————- 178kN (20 tons)
- Compact Desch-Lutex clutch brake unit
- Press stroke length ———————– 19mm, 0.75″
Dieset area dimensions: |
(millimeters) |
(inches) |
---|---|---|
Throat height | 406 | 16 |
Throat depth from press centerline | 356 | 14 |
Dieset base plate length | 337 | 13.25 |
Dieset base plate width | 457 | 18 |
- Shut height ——- 169mm (6.6″)SDAU, to 142mm (5.6″)SDAD
- Preloaded linear roller bearings in light weight aluminum slide
- Under slide adapter is easily changed out to mate with specific customer diesets adjustable height dieset base permits compensation for die grinding
- 3.7kW (5.0HP) (460/60/3) main press flywheel motor
- 5.5kW (7.5HP) variable speed drive for flywheel motor
- Press stroking speed ———————– 200-1100 spm
Safety equipment:
- Interlocked flywheel guard
- Press brake monitor
- Double safety valve for main press clutch brake unit
- Anti-tie down anti-repeat module in press start circuit
- Machine E-stops
- Main electrical disconnect with lockout
- Main air supply disconnect with lockout
- Point of operation guard is furnished to protect operating personnel near the dieset. This can be either: a Gordon Proxagard system (offered as standard), physical barrier guard (optional), full light curtain system (optional)
Utilities required at customer plant:
- Electric power, 480 volt 60 Hz 3ph 25 amp service, or 400 volts 50 Hz 3ph 30 amp service
- Clean dry compressed air at minimum of 4.7 bar (70 psig) and 0.7 standard cubic meters per minute (24 scfm).
Options:
- Material handling systems
- Scrap conveyor
- Sound reduction enclosures
- Slot diesets
Robotic feeders
We introduce the Positech Press Tender®, a double tooled SCARA robot based feeder, that handles laminations for notch and separate operations.
Features:
The Press Tender® capable of handling 0,6mm thick lamination blanks up to 1000mm diameter.
- When configured to process typical lamination (870mm diameter), cycle times are 5 seconds to notch, and 3 seconds to unload & reload the notching press. Product yield is 400 pieces per hour and 3200 per 8 hour shift, calculated at a modest 90% machine run time.
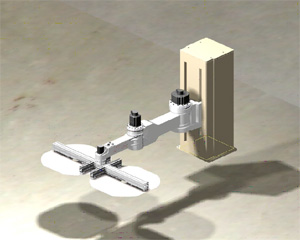

Specifications:
- The equipment furnished includes the following:
- Robot and all controls
- All tooling required to handle incoming blanks and notched laminations
- Physical perimeter fencing and optical presence sensing safety devices for personnel protection
- A teach pendant with safety controls is provided that can also be used to program the robot. Different lamination size can be fed using the teach pendant in a training mode; no code writing is required. Once the end positions and profiles are taught, they are permanently saved for use in the future.
Column 1 | Column 2 | Column 3 |
---|---|---|
Arm length | Full length | 59 in. (1500mm) |
Axis 1 (large rotation) | 33.5 in. (850mm) | |
Axis 2 (medium rotation) | 25.6 in. (650mm) | |
Working Envelope | Axis 1 | ±110° |
Axis 2 | ±150° | |
Axis 3 (up and down) | 23.6 in. (600mm) | |
Axis 4 (smallest rotation) | ±360° | |
Maximum Speed | Axis 1 | 130° / s |
Axis 2 | 160° / s | |
Axis 3 (Z axis) | 39.4 in (1000mm) / s | |
Composite | 206 in.(5.22M) / s | |
Axis 4 (Z axis rotation) | 300° / s | |
Load | Maximum payload wt. | 154 lbs. (70kg) |
Maximum Moment of Inertia | 31 lb.-in.-s2 (3.5kgm2) | |
Positioning repeatability | X, Y (Plane) | ±0.008 in. (0.2mm) |
Z-axis (Vertical) | ±0.008 in. (0.2mm) | |
Axis 4 (Z-axis rotation) | ±0.05° | |
Robot Weight | 1210 lbs. (550kg) |
Servo indexers
General:
To date, Positech has upgraded over 50 notching presses with the Compuslot® servo-indexer. Compuslot® is a versatile improvement that often is included with new controls for older presses. Compuslot® has been installed on the following press brands:
- V&O
Schuler
- Minster
- Muller Weingarten
- Comessa PDG